Coffee solutions
GRAND COFFEE SOLUTIONS SA

Written by: Prosilias George - Director of Quality Assurance and Quality Control
Company overview
Processing, packaging and coffee trade.
Trade of standardized related products of coffee, tea and chocolate beverages.
Challenge
The company was in need to ensure quality and safety at every stage of the production and storage process. Specifically, key needs include:
- Continuous monitoring of conditions: The company needs to continuously monitor critical parameters, such as temperature and humidity, to maintain the quality of raw materials and finished products and reduce the risk of spoilage
- Immediate reaction to deviations: The ability to react immediately to any deviations from the desired conditions was important to prevent losses and avoid impacts on product quality. With the real time temperature and humidity data loggers, the company can receive real-time alerts to prevent problems
- Automated recording and compliance: The company needs a solution that automatically records environmental conditions, providing evidence of compliance with quality standards and certifications. This recording helps support audits by authorities or customers and facilitates product quality certification.
- Time and resource savings: the need for an efficient and automated inspection process, without the need for physical presence, helps to reduce costs and save labor time. The remote monitoring capability fully meets this need
- Preventive maintenance: The need to prevent potential problems before they develop into malfunctions or losses has made the use of loggers important. The possibility of predictive maintenance and analysis ensures the stability of conditions in the production and storage areas
The installation of HAM Systems' loggers provided comprehensive solutions for all of these needs, enhancing the company's overall efficiency and quality assurance.
Solution
The installation of HAM Systems' real time recorders in the production and storage areas of products meets critical monitoring and quality assurance needs, offering solutions that enhance our efficiency and reliability. Specifically, these recorders offer us:
- Continuous monitoring of parameters such as temperature, humidity and other critical environmental conditions. This enables full compliance with required safety and quality standards
- Immediate notifications via mobile or computer alerts when any value deviates from the predefined limits or if any equipment is switched off. This allows us to react immediately to possible deviations and prevent problems
- Remote access and real-time monitoring, allowing us to check conditions at any production or storage site directly from my mobile phone or tablet, regardless of location
- Automated data logging and analysis, giving us transparency and the ability to check historical conditions, with records that can be used for documentation and compliance with quality control and safety requirements
- Predictive and preventive maintenance capability, as analytics and alerts can identify trends that indicate potential problems before they affect the process
These solutions offer an advanced level of control and safety, allowing us to enhance the quality and integrity of our products at every stage of production and storage.
Feedback
Since we installed the HAM Systems devices, we have seen a significant improvement in the way we monitor production and storage conditions. The feeling we have had using the loggers is extremely positive, as they fully meet the requirements for continuous quality and safety control. Your platform has proven to be reliable and easy to use, facilitating both immediate real-time monitoring and remote access from mobile devices. This enables us to maintain constant control of conditions wherever we are. The lessons learned from our work with your company have been extremely positive. The alerts in case of deviations from predefined limits help us to prevent problems before they become serious, and the automation of data logging has significantly improved the accuracy and reliability of our documentation.
The support we receive from your team is also one of the great advantages of our cooperation. Whenever a question or concern arises, the response is prompt and efficient, solving our needs quickly and clearly. Your ongoing support has reinforced our confidence in the platform and its capabilities. Overall, our experience with HAM Systems' devices and platform has exceeded our expectations and certainly met our requirements for a reliable and efficient monitoring solution.
Indicative photos from the installed equipment
Why HAM Systems?
Remote Monitoring
HAM Systems' Wi-Fi temperature data loggers are designed with a focus on commercial cold storage.
With our Wi-Fi temperature data loggers you can have see the conditions of your cold storage from anywhere in the world using your phone, at any time.
Health inspection reports
Save time (=money) from handwritten logging. The HAM platform logs data 24/7 for years with no monthly fees.
Export reports in pdf and csv for any date and step. Print temperature history for health inspection in less than 1 minute!
Instant Alerts
Our system will immediately alert you if something goes wrong with a push notification, email, SMS or even a call to your phone!
Easy setup, scalable
Setup is so easy, that in many cases you don't even need a technician.
All you need is a Wi-Fi network with Internet connection. Our Wi-Fi temperature data loggers connect directly to our Cloud, no centrals hubs required!
Customer Support
It signifies a commitment not just to providing a product, but to ensure
that the product truly meets and exceeds the needs and expectations of
its users. It entails offering strong after-sales support, listening to
feedback, and constantly iterating on products to better serve the
customer base.
HAM Systems
HAM ThermoSenseX1 - WiFi temperature data logger with alerts
VAT not included in price

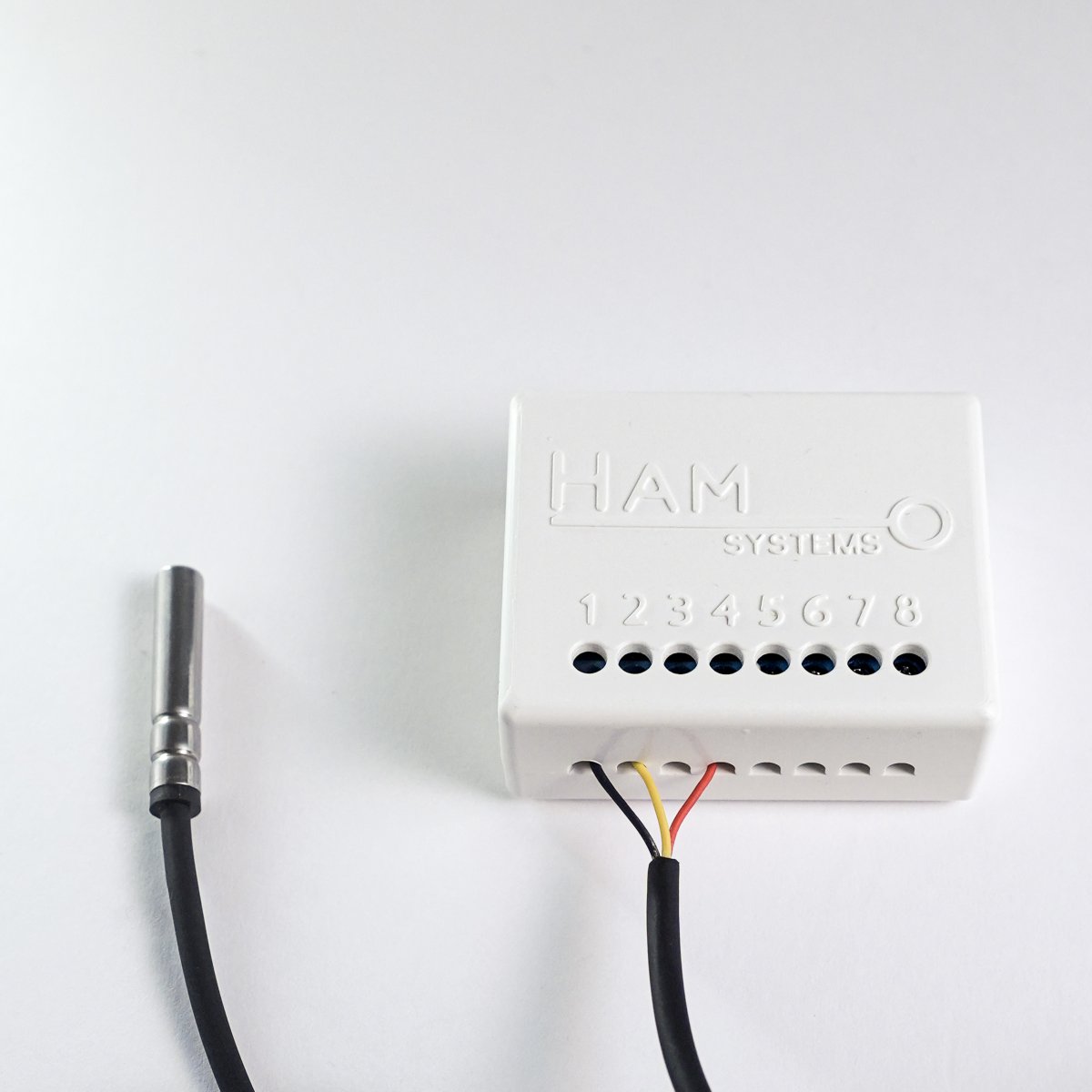
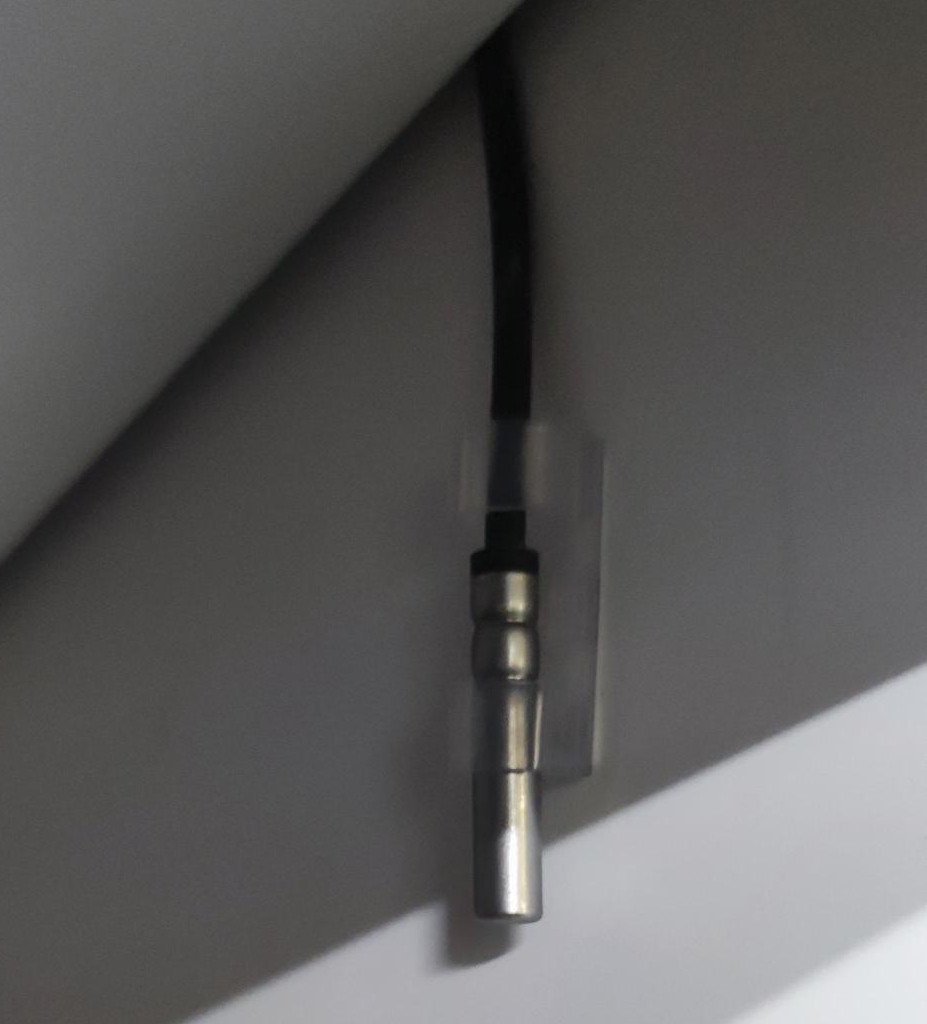
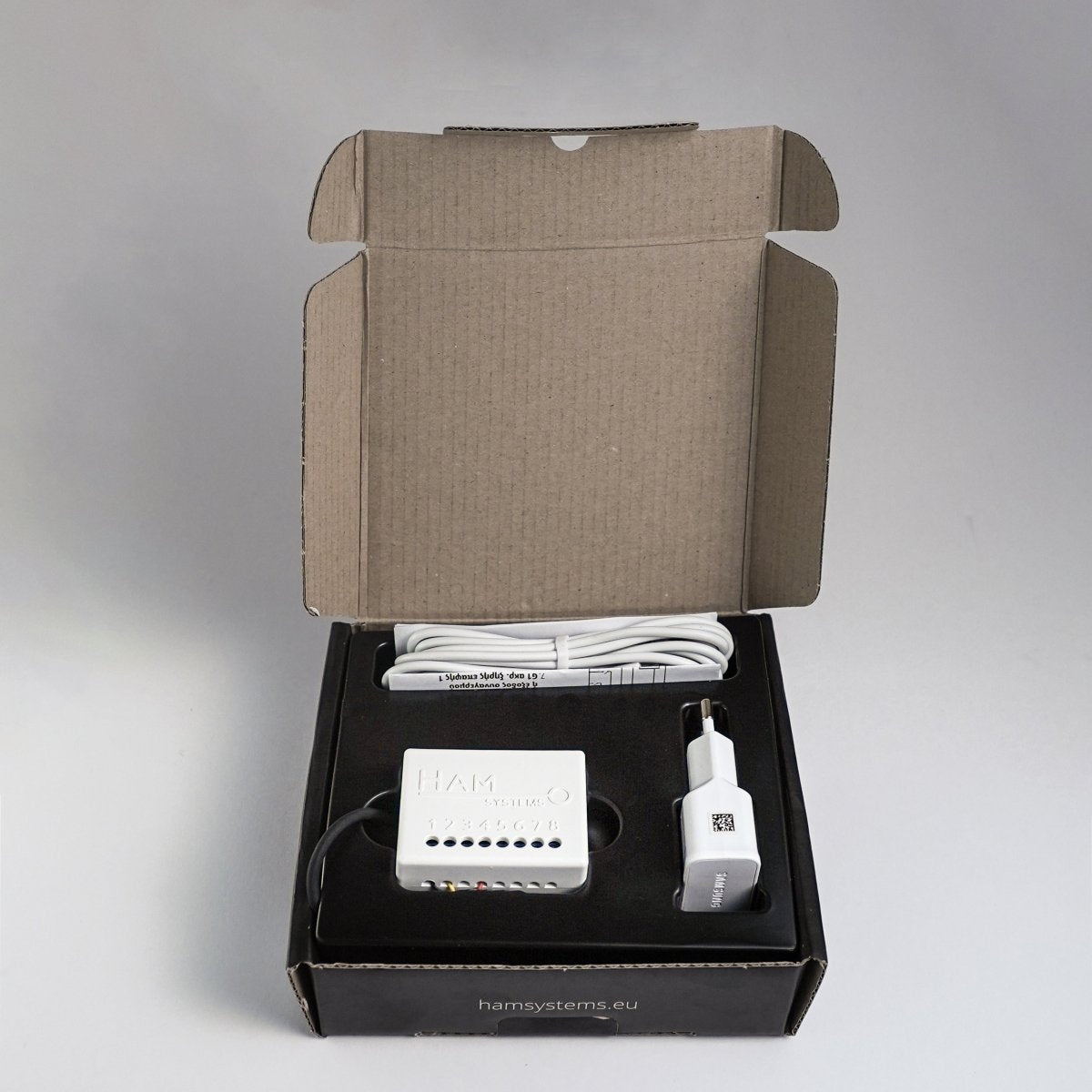